切削刀
- 网络cutting blade;The Cutting Edge;bite
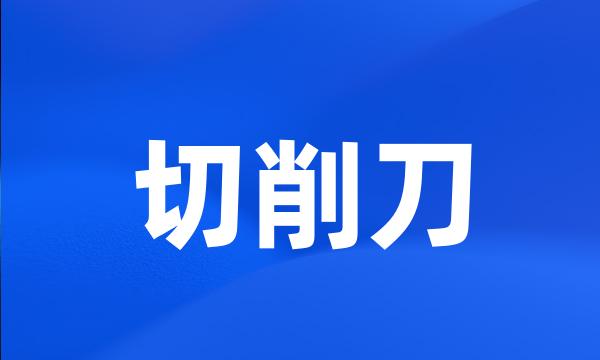
-
软土地基土压平衡盾构切削刀盘扭矩的计算
Torque Moment Analysis of Earth Pressure Balanced Shield Cutter Head under Soft Foundation
-
拖板是切削刀在需要的进料装置方向的机制。
The carriage is the mechanism feeding the cutter in the needed direction .
-
与通用切削刀一起结合形式切削刀也是可能的。
It is also possible to combine form cutters along with general purpose cutters .
-
然而,这不减去从这颗独特宝石切削刀的爱。
However , this does not detract from the cutters'love of this unique gem .
-
导电加热切削刀-工接触区的电传导模型及状态的研究
On the Model and State of Electric Conduction in Tool-Workpiece Contact Zone in Electric Hot Machining
-
钳工切削刀的典型结构及在生产中的应用盾叶薯蓣发酵生产2,3-丁二醇及其双水相萃取研究
Typical Structure of Tool for Benchwork Microbial Production and Aqueous Two-phase Extraction of 2,3-Butanediol from Dioscorea Zingiberensis
-
因此所有切削刀应该在大小上是相似的和考虑到的形状更大的速度和饲料。
Hence all the cutters should be similar in size and shape to allow for larger speeds and feeds .
-
方法:采用美国117型准分子激光仪联合自动微型板角膜切削刀使角膜曲率发生改变,从而改变角膜屈光度,提高视力。
Methods : Applying America-made 117 type excimer laser instrument combined with automatic miniature lamina cutter for cornea to change corneal curvature and diopter to improve visual acuity .
-
盾构前端有一个全断面切削刀盘,切削刀盘后面有一个贮留碴土的密封舱,在密封舱底部装有长筒形螺旋输送机。
With a whole section cutting-plate in the front end , a sealed cabin is formed to deposit the soil , at the bottom of which a screw conveyor is equipped .
-
金属切削过程刀&屑接触区摩擦状态有限元分析
Finite Element Simulation of Friction on Tool-Chip Interface in Metal Cutting Process
-
金属切削中刀-屑接触长度的有限元分析
Finite Element Analysis for Tool-chip Contact Length in Metal Machining
-
高速切削的刀位路径规划与控制策略
High Speed Cutting Path Planning and Control Strategy
-
最后,根据参与切削的刀齿分布情况求解出铣削微通道时的切削力模型。
Finally , Cutting force model of milling microchannel is established according to the distribution of all the teeth participating in cutting simultaneously .
-
证实了振动切削前刀面摩擦状态的改善对切屑的形成有很大的影响。
The results are proved to good by many experiments and it is also proved that the frictional force on the tool face has great influence on chip formation .
-
同时,运动学的分析工作,也为动力学分析、杆长相互关系的组合与选择、切削机构刀盘位置布置及结构设计等分析提供了前期的理论分析基础。
Kinematics analysis provides prophase theoretical fundament for analysis of dynamics , choice and combination of bar length , position of cutters , design of structure , and so on .
-
SiCp增强铝基复合材料切削加工中刀-屑摩擦模型及其磨损性能研究
A Study on a Friction Formula between Tool and Chip and Wear Characteristics when Cutting SiC Reinforced Aluminum Composite
-
限制接触刀具切削力与刀&屑接触长度关系的研究
Study on Relationship Between Cutting Forces and Contact Length of Restricted Contact Cutters
-
金属切削加工中刀&屑紧密型接触长度的研究
Study on Tool-chip Close Contact Length in metal cutting
-
振动切削过程中刀头的振动分析石材切割锯片金刚石刀头磨损状况的研究
An analysis on the tool vibration during vibration cut study on wear of diamond sawblade segment
-
用连续激光测试技术测量了切削过程中刀楔内的应力分布规律;
In this paper , the tool tip mechanical stress distribution in a cutting process is studied with continuous laser measuring technique .
-
并以该刀具轨迹进行叶片切削过程、刀位轨迹及机床运动的动态仿真。
The cutting process of blade , position of cutter and movement of machine tool dynamically was simulated by the track of cutter .
-
导电加热切削时,刀-工导电回路的状态与常规的电流回路有所不同。
The state of circuit of tool and workpiece in Electric Hot Machining ( EHM ) is different from that of conventional circuit .
-
对比锯切实验中的切割电流、切割速度等参数。检测经过切削后的刀头中的金刚石颗粒的磨粒破坏形态及出刃高度。
The cutting current , cutting speed of the sawing experiments , damage morphology of diamond particles in the blade after cutting abrasive and protrusion height are compared .
-
硬质合金刀具在不锈钢加工中,其刀具耐用度主要是取决于后刀面边界磨损而不是主切削刃后刀面的平均磨损量。
In many cases of stainless steel cutting operations with carbide tools , a tool life strongly depends on flank notch wear of depth of cut rather than average flank wear of main cutting edge .
-
切削过程中扎刀现象的理论分析及其预防措施
Theoretical Analysis and Preventive Measures for " Breaking Edge " Phenomenon in Cutting Process
-
最后,对切削速度、后刀面磨损和切削深度对残余应力分布的影响规律进行了分析。
At last , the influences of cutting speed , flank wear and cutting depth on residual stress are discussed .
-
数控加工工艺优化一般包括:刀具、切削参数、走刀方式的选择,刀轨路径的生成等方面。
The optimization of CNC machining typically includes : the selection of tools , cutting parameters and tool moving styles ; the generation of cutting-path and so on .
-
该方法能精确成形群钻复杂切削刃的后刀面,加工过程简单且易于操作。
All kinds of cutting edges'flank of the multiface drills can be produced exactly by this method , and the producing process is simple and easy to be operated .
-
在此基础之上,根据风电机轮毂各加工面的特点设计了专用切削刀具、专用刀库及钻模。
Above this foundation , designed the special cutting tools , the special tool magazine and the drilling model according to the characteristics of each working surface on the workpiece .
-
本文对异形盾构切削机构提出了刀盘工作点及驱动装置与五杆机构的几种不同布置形式,以供在实际的机构设计中选择最佳结构布置方案。
Working point of cutter head and layout style of driving apparatus and five-rod mechanism is brought forward in this paper . It is very useful for selecting best layout diagram in actual structure design .