乳化液
- 名emulsion
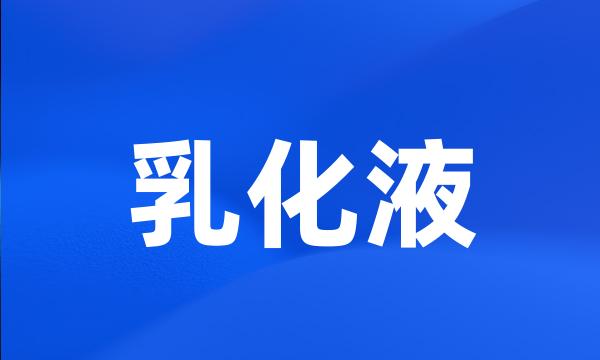
-
参数化乳化液泵CAD系统的研究
Research on Parametric CAD System of Emulsion Pump
-
基于PLC的乳化液泵智能监控系统研制
Research and Contruction Emulsion Pump Station Intelligent of Monitor System Based on PLC
-
PASS对冷轧高浓度含油乳化液废水的复合絮凝处理
Composite Flocculating Treatment of Cold - rolling High Concentration Emulsifying Wastewater by PASS
-
O/W型乳化液的处理
Treatment of an O / W Emulsion Wastewater Treating Wastewater
-
最后用VISUALBASIC6.0将乳化液泵站故障诊断系统以友好的界面展现给用户。
The system of the fault diagnosis of emulation pump designed by visual basic 6.0 is displayed to users with friendly interface .
-
CO2乳化液强化置换水合物中CH4的作用研究进展
Research progress in the enhanced replacing methane out of gas hydrate by carbon dioxide emulsion
-
啤酒中的硫化物探讨了含硫乳化液在极压状态单分子反应层生成的速率,乳化液比乳化油有较高的Pb极压值;
Sulphide in Beer The reacting speed of a layer sulphide is investigated under extreme pressure condition .
-
LiBr溶液浓度测量软件系统设计矿用乳化液浓度自动检测方法的研究
The software system design of concentration measurement of LiBr aqueous solution
-
因为电混凝后出水pH较高,含一定量的NaNO2,重新配制乳化液时,就可以节省NaNO2。
So we can circularly make use of treated effuent by electro coagulation . Because the effluent contains some NaNO 2 in high pH , we may save NaNO 2 .
-
此外,酶解产物上清和沉淀乳化液的ESI增大。
Furthermore , ESI value of the hydrolysates were increased .
-
叙述了SOW乳化液的不稳定现象,并讨论了一些稳定化的途径。
The phenomenon of instability for SOW emulsion was described , and the way for stabilization was discussed .
-
方法:选SD系大鼠60只,取大鼠胃粘膜匀浆液加入弗氏佐剂制作成乳化液,注射入大鼠体内进行免疫。
Methods : 60 SD rats were used and the rat 's gastric membrane was made into emulsification solution so as to immunize the rats .
-
利用蜂蜡(BW)和月桂酸(La)对SPI膜进行共混改性,在形成乳化液的基础上形成SPI/脂类膜。
Blend-modification of soy protein isolate solutions with beeswax and lauric acid ( La ) to has been used to form SPI / lipid emulsion edible films .
-
利用环块磨损试验机在不同载荷下对热喷涂Al2O3-TiO2复合陶瓷涂层的乳化液润滑滑动磨损特性进行了研究。
The sliding wear behavior of thermal-sprayed Al2O3-TiO2 ceramic coating has been investigated with a ring-on-block wear tester under different loads in emulsion lubrication sliding .
-
以司班-80(Span-80)与吐温-20(Tween-20)为复合乳化剂,将轻质石油产品分散成均匀的油水乳化液。
Dissipate light petroleum into uniform oil-water emulsion using Span-80 and Tween-20 as complex emulsifier .
-
该方法以Venturi流量计测量原理为基础,利用Bernoulli方程计算出所配制乳化液油水质量比。
The method is based upon the mechanism of Venturi meters , the quality ratio of oil to water can be calculated from Bernoulli equation .
-
用高速动态分析仪测量不同含水率β下,滞止油水乳化液中弹状流流型时Taylor气泡的漂移速度。
Taylor bubbles drift velocity at various rates of water content in stagnant oil water emulsion and under a slug flow regime was measured with the use of a high speed dynamic analyzer .
-
以PVA水溶液作为水相,PCL氯仿溶液作为油相,司盘80为乳化剂,制备W/O型的PVA/PCL均匀乳化液。
W / O type of PVA / PCL uniform emulsion was prepared with PVA aqueous solution as water phase , PCL chloroform solution as the oil phase , and Span 80 as emulsifier .
-
只有稳定性适中、且含有适量HLB值较高的阴离子型表面活性剂作乳化剂组分的半透明细乳化液,才具有最佳的防锈性能和缓蚀性能以及较好的稳定性。
Only the semi transparent emulsion which has moderate stability and contains appropriate quantity of high HLB value anion surfactant has both optimal rust prevention , corrosion inhibition and stability .
-
自动液面控制器(用于轧车的轧槽)CO-1冷轧铜带乳化液与轧制润滑效果
Automatic liquid level controller CO-1 Cold Rolling Emulsion Oil for Copper Sheet and Lubrication Performance
-
较佳的聚合工艺为:种子聚合温度80℃,预乳化液滴加时间15h;壳层聚合温度75~80℃,滴加时间5h。
The preferred polymerization conditions were that seed polymer temperature 80 ℃, pre-emulsion distribution droplets time 1.5 h , shell polymerization temperature 75 ~ 80 ℃, distribution droplets time 5 h.
-
在此基础上,通过Plackett-Burman设计,对影响其产酶的11个相关因素进行了评估,筛选出具有显著效应的三个因子:橄榄油乳化液浓度、豆饼水解液浓度及初始pH值。
Based on the result , screening design methodology Plackett-Burman was used to evaluate the eleven factors related to lipase production , and three statistically significant factors ( soybean cake meal , olive oil , and initial pH ) were selected .
-
本课题研究的是经物化破乳后的废乳化液,其COD值高达几万,成分复杂,难降解,国家列其为危险废弃物。
The object of the subject is waste emulsion by the physical and chemical emulsion of breaking , the COD value reach up to tens of thousand , the composition is complicated , and difficult to break down , our country delimits that it is hazardous waste .
-
实验结果表明:乳化液废水经孔径为200nm的无机陶瓷膜处理后,透过液可达国家排放标准;
The results show that emulsified fuel can be removed basically with 200 nm inorganic ceramic membrane , and the infiltration liquid reach the national discharging standard .
-
试验中对混凝气浮和混凝沉淀进行了对比,试验结果表明:对于含油乳化液废水,气浮法对浊度、COD和油的去除率可分别高达99.5%、99.3%和99.9%,高于沉淀法;
Air flotation and sedimentation were contrasted at the course of the experiment , the experimental results show that the removal rate of the turbidity , COD and oil that by air flotation is high as 99.5 % , 99.3 % and 99.9 % respectively and higher than of sedimentation ;
-
针对本钢冷轧厂CDCM机组乳化液系统使用中,撇污装置、供给泵、磁性过滤装置存在的问题进行了改造。
In accordance with the problem on the skimmer , supply pump , magnetic filter during operation , the modifications of the emulsion system of CDCM unit are made .
-
综合考虑加工效率、加工质量、成本及环保等因素,在自来水中配制5%体积浓度的DX-1乳化液是比较理想的工作液。
Considering processing efficiency , processing quality , cost and environmental factors , 5 % vol. DX-1 oil water emulsion is the ideal working fluid .
-
本文用柴油和水超声乳化液作为原料液,模拟实际含油水体,设计了柱高0.9m的微孔管浮选柱。
Diesel and water phacoemulsification was used to simulate the industry oil-containing water as raw material liquid . The flotation column was designed to be 0.9m high .
-
介绍一种适用于不锈钢抛光用的ZH-1抛光乳化液,该液具有抛光、润滑、防锈和冷却等多种功能;
A type of ZH-1 emulsified polishing solution suitable for the polishing of stainless steel is introduced , which has the multifunctions for polishing , lubricating , anti-rusting and cooling .
-
优化制备的CuOγ/-Al2O3催化剂用于处理高浓度难降解的乳化液废水时具有良好的催化活性,在200℃时反应2h,TOC去除率为81.3%,比未加催化剂的湿式氧化提高了14.9%。
The prepared catalyst of CuO / γ - Al_2O_3 which had good catalytic activity was applied in the treatment of emulsification wastewater , and resulted in 81.3 % TOC removal after 2 h oxidation at 200 ℃, which brought about improvement of 14.9 % , compared to non-catalytic oxidation ;