摩擦表面
- 名friction surface
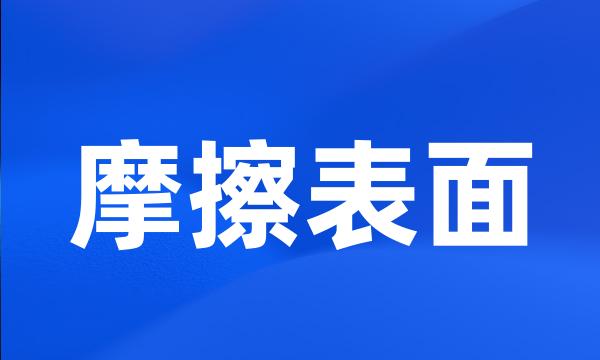
-
纳米Cu添加剂润滑摩擦表面分析
Analysis of Friction Surface Lubricated with Nano-Cu Additive
-
这一现象是与在摩擦表面上形成含S,P和Zn的表面反应膜有关。
According to the friction surface analysis , this phenomenon is concerned with the surface reaction film containing S , P and Zn .
-
采用K射线光电子能谱仪对摩擦表面进行了分析,并探讨了添加剂的抗磨作用机理。
The rubbed surface was investigated using X-ray photoelectron spectroscopy , and the antiwear mechanism was discussed .
-
纳米Fe2O3颗粒填充UHMWPE复合材料摩擦表面的原子力显微分析
AFM analysis of micro-wear mechanisms in nano-Fe_2O_3 particle reinforced UHMWPE composite
-
文章还对DE成膜剂在摩擦表面上形成的摩擦聚合膜的作用机制进行了分析和探讨。
The functional mechanism of friction polymeric film formed on the friction surface was also discussed .
-
摩擦表面MoS2润滑膜的显微结构分析
Microstructure analysis of lubricating mos_2 film formed on frictional surface
-
MoS2摩擦表面氧化与电子转移
Surface Oxidation and Electron Transfer of MoS 2 During Friction
-
这种膜含有Fe元素,表明它是摩擦表面作用后产生的。
But there is Fe element in this thin film , it is resulted from the mutual action between two friction surfaces .
-
摩擦表面的SEM形貌显示,钢/铜纤维摩擦材料的摩擦表面主要由铜纤维涂抹形成的大块不连续的摩擦膜组成;
Discontinuous pieces of friction film formed on the surface of the Steel / Cu fiber reinforced material due to the smearing of Cu fibers .
-
与Ⅰ相比较,Ⅱ的分子使活性元素P、S更容易进入摩擦表面,促进表面膜的形成和稳定。
Compared with the ⅰ, the ⅱ makes the active elements P and S. more easily to be located on the surface film thus lead to the formation and stabilization of the surface film .
-
摩擦表面生成由富C层和过渡层组成、厚度250~450nm左右且分布不均匀的修复改性层,初步推测其中富C层为类金刚石结构;
A 250 ~ 450 nm repaired layer with a carbon-rich layer and a transition layer was unevenly distributed on the frictional surface . The carbon-rich layer was supposed as in DLC structure .
-
水润滑条件下,摩擦表面产生了Si(OH)4反应膜,降低了磨损,主要是化学腐蚀磨损。
Under water lubrication , the film of Si ( OH ) _4 is found on the friction surface . The worn surfaces characterized by chemical fretting wear .
-
电镜能谱分析表明,硫磷型复合极压剂水溶液在摩擦表面与Fe发生化学反应,生成一种含硫磷的化学反应膜。
SEM analysis indicated that the S-P type EP agent added in water could form a chemical reation film with Fe which contained S and P on the rubbing surface .
-
Fe3Al基复合材料摩擦表面的分形特性研究
Fractal Characteristics of Friction Surface of Fe_3Al-based Composites
-
随着pv值的增加,涂层摩擦表面温度升高、破坏加剧,故摩擦系数和磨损质量损失增大;
The sliding surface temperature and damage increased with increasing PV value , thus the friction coefficient and wear mass loss increased aw well .
-
纳米粒子在摩擦表面的沉积是SnO纳米粒子改善润滑油摩擦学性能的内在机制。
Deposition on friction surface of SnO could make the tribology of Lubricating oil better .
-
磨损机理研究表明,SiC/Si复相材料的磨损机理为摩擦表面的氧化水解及微区断裂剥落。
The wear of SiC / Si composite was characterized by the oxidation of SiC and Si on the worn surface of SiC / Si composite and micro-fracture and spalling .
-
采用金相、扫描电镜、X射线衍射、拉曼光谱等手段对不同试验条件下的摩擦表面、磨屑的形貌与结构进行了检测,探讨了C/C复合材料的磨损机理。
In order to inquire into the worn mechanisms , the morphology and structure of worn surfaces and wear debris were examined through using optical microscopy , scanning electron microscopy , X-ray diffraction , laser Raman micro-spectroscopy .
-
扫描电镜对摩擦表面和抗弯断口的对比观测表明,ZrO2增韧Al2O3陶瓷磨损破坏机理属于一次性脆性断裂机理。
The observation of friction surface and bending Fractured surfaces by means of SEM shows that wear failure mechanism of ZTA ceramics belongs to brittle fracture mechanism .
-
表面分析结果表明,油溶性纳米Cu添加剂能够降低摩擦表面的显微硬度,并显著改善磨损表面的形貌。
Surface analysis on the worn surface indicated that the microhardness of friction surface could be reduced and the state of worn surface could be obviously improved by adding the oil-soluble nano-Cu additive .
-
PBC作为一种摩擦表面改性、修复剂,因其特殊的作用机理,从而表现出较为显著的减摩抗磨特性。
As a type of friction surface modifier and recondition agent , PBC had good reduced friction and abrasion resistance .
-
利用扫描电镜(SEM)对聚四氟乙烯基固体润滑剂摩擦表面及在45钢表面所形成的润滑转移膜形貌进行表征;
The polytetrafluoroethylene ( PTFE ) - based bonded solid lubricant coating and the surface of lubricating metastasis membrane forming on the surface of 45 # steel were detected using scanning electron microscope .
-
这是由于在低速下,SiO2易凸出摩擦表面而增加材料的磨损,而在高速下由于硬质SiO2颗粒对摩擦膜起到很好的钉扎作用而使其摩擦系数增加,磨损率降低。
SiO_2 easily moved onto surface and increased wear at low speed , but it pinned tribo-film and so increased friction coefficient and decreased wear rate at high speed .
-
钢球磨斑表面元素EDS分析表明,在极压条件下,二聚酸钾与摩擦表面发生某种磨擦化学反应,形成了一层有机类抗磨膜。
EDS analysis of wear scar showed that dimer acid potassium might react with rub surface and form an organic anti-wear film on extreme pressure condition .
-
EDAX能谱仪分析表明,该产物的抗磨性能与摩擦表面中存在硼、氯活性元素有关。
EDAX Spectroscopy analyses shown that anti-wear properties of this additive were related to Cl , B active elements existed on rubbing surface .
-
钢球磨痕表面的AES分析结果表明,有机硼化物减摩剂主要是通过在摩擦表面分解形成含硼的氧化物膜而起减摩作用。
The results of AES analysis of the frictional surface indicated that the friction reducing agent decomposes to form a film containing boron oxide on the frictional surface to give the friction-reducing properties .
-
当pv值足够大时,涂层摩擦表面温度进一步升高,部分涂层发生熔融并形成润滑膜,相应的摩擦系数和磨损质量损失降低。
At a high enough PV value , the sliding surface of the coating would experience local melting and form some kind of lubricating film , hence the friction coefficient and wear mass loss increased .
-
用俄歇能谱(AES)、X-射线衍射(XRD)、扫描电镜(SEM)及X-射线能谱(EDX)研究了摩擦表面元素组成及其可能物相。
Auger electron spectroscopy ( AES ), X-ray diffractometer ( XRD ), scanning electron microscopy ( SEM ) and X-ray dispersive spectroscopy ( EDX ) were employed to study the elemental distributions and their possible phases in the .
-
当pv值较低时,涂层摩擦表面温度相对较低,涂层仅发生弹性变形,相应的摩擦系数较小;
The nylon-1010 coating was dominated by elastic deformation at a smaller PV value which corresponded to a lower sliding surface temperature , thus the friction coefficient and wear mass loss were smaller in this case .
-
通过DSC和PGC对摩擦表面和摩擦副表面进行成分分析,揭示了PA-6/PE合金摩擦性能优良的原因。
In order to study the friction mechanism of PA-6 / PE alloy , DSC and PGC are used to analyse the composition of the material on the PA - 6 / PE alloy friction surface and its counterface .