涵道比
- 网络bypass ratio;by pass ratio
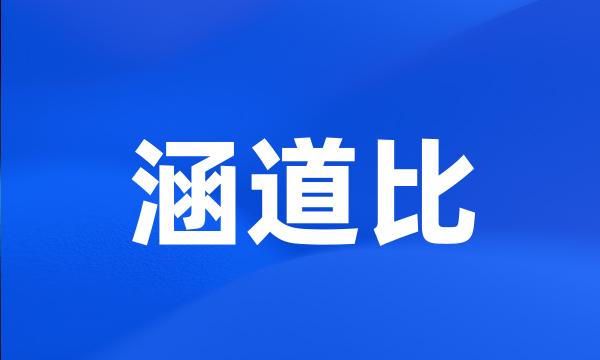
-
计算结果表明,低压涡轮和混合器的调节对发动机的性能和涵道比的影响尤为显著;
The results of calculation show that the adjusting of low-pressure turbine and mixer has a remarkable effect on the performance of engine and bypass ratio .
-
为正确使用和推广减推力起飞技术,分析了高涵道比涡轮风扇发动机温度特性和大型民航机起飞性能。
For correct and wide application of reduced thrust takeoff technique , the temperature characteristics of high bypass ratio turbofan engines and the takeoff performance of large aircrafts were analyzed .
-
发展了一种低涵道比混合排气加力涡轮风扇发动机接通加力时的数值模拟方法。
Numerical simulation of turbofan engine afterburner light-on process was presented .
-
现代高涵道比涡扇发动机关键技术
Key Technology of Modern High Bypass Ratio Turbofan Engine
-
大涵道比涡扇发动机涡轮结构设计关键技术分析
Analysis of Key Technologies of Turbine Structural Design for High Bypass Ratio Turbofan Engine
-
因此低叶尖切线速度是将来大涵道比风扇的发展趋势。
Therefore , the low tip tangential speed design of high bypass ratio is a trend .
-
较为系统地总结了国外大涵道比涡扇发动机的研制特点和设计特点。
The development and design features of the high bypass ratio turbofan engine in foreign are comprehensively summarized .
-
通过一个高涵道比涡扇发动机故障诊断的实例分析,验证了三层逆传播网络的可行性。
The case study of a high bypass ratio turbofan engine has verified the feasibility of a three-layer back propagation network .
-
以发展大涵道比涡扇发动机为例,说明了约束条件对设计循环参数的限制。
As an example , the development of a high bypass ratio turbofan engine was used to demonstrate how the constraints restrict design cycle parameters .
-
建造更加环保型的喷气发动机还可另辟蹊径:增大发动机的涵道比(注1),采用开放转子的结构。
There is another way to build a greener jet engine : by bypassing the turbine to an even greater extent , with an open rotor .
-
得到:(1)其必为变涵道比循环系统,由可变几何内、外涵通道提供对涵道比的主动控制;
Therefrom some conclusions are obtained as : 1.The system 's bypass ratio must be actively controlled by adjusting both core and bypass engine 's through flow areas .
-
结果表明宜采用小涵道比涡扇发动机,而且不考虑费用时涡轮前温度取值越高越好,考虑费用时则有最大值;
The results show that a turbofan engine with a small bypass ratio must be installed , and a suitable turbine entry temperature is obtained by optimization with life cycle cost .