超高温合金
- 网络supertherm
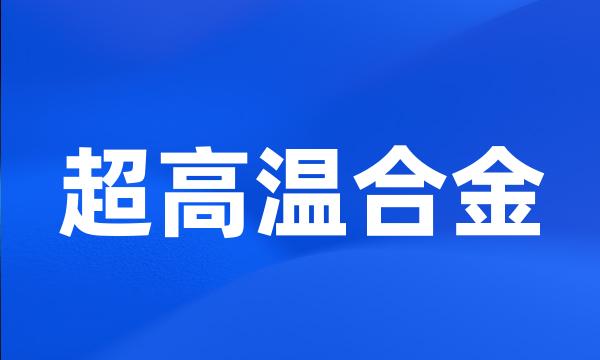
-
铌硅化物基超高温合金包埋渗Si层的组织形成及高温抗氧化性能
Microstructural Formation and High Temperature Oxidation Resistance of Pack Siliconized Coatings on an Nb Silicide Based Alloy
-
新型Nb硅化物基超高温合金的氧化行为及其抗氧化涂层技术研究
Oxidation Behavior of an Advanced Niobium-Silicide Based Ultrahigh-Temperature Alloy and Preparation of Its Oxidation-Resistant Coatings
-
高温热处理对Nb硅化物基超高温合金组织特征的影响
Effects of High Temperature Heat Treatments on the Microstructure of an Nb Silicide Based Ultrahigh Temperature Alloy
-
铌硅化物基超高温合金Si-Y2O3共渗涂层的组织及其高温抗氧化性能
Microstructure and High Temperature Oxidation Resistance of Si-Y_2O_3 Co-deposition Coatings Prepared on Nb-silicide-based Ultrahigh Temperature Alloy by Pack Cementation Process
-
利用真空自耗电弧熔炼法制备了三种成分的Nb硅化物基超高温合金。
Three Nb-Si based ultrahigh temperature alloy ingots with different nominal compositions were prepared by vacuum consumable arc-melting .
-
Ti-Nb-Si基超高温合金Si-Cr共渗抗氧化涂层的显微组织
Microstructures of Si-Cr co-depositing coatings prepared on Ti-Nb-Si based ultrahigh temperature alloy
-
铌硅化物基超高温合金电弧熔炼态组织和成分分布
Microstructure and Compositional Distribution in Arc-melted Advanced Nb-silicide-based Ultrahigh Temperature Alloy
-
铌硅化物基超高温合金整体定向凝固组织和固/液界面形态演化
Microstructure and solid / liquid interface morphology evolution of integrally directionally solidified Nb-silicide-based ultrahigh temperature alloy
-
结合国内外共晶自生复合材料常用的制备技术,提出了适用于铌基超高温合金整体定向凝固技术的坩埚材料及其涂层技术。
Based on the common manufacturing technology of in-situ composites at domestic and abroad , the crucible materials and the coating technologies suitable for the whole directional solidification technique of niobium based ultrahigh temperature alloys are proposed .
-
直径2000mm超大型高温合金涡轮盘的制造工艺研究
Research on production of φ 2000 mm super large gas turbine disk of Superalloy
-
耐超高温铱合金强韧化技术研究进展
Research Progress in Strengthening and Toughening Technology of Iridium Alloys for Ultra-high Temperature Application
-
生长速率为10μm/s的超高温梯度Fe83Ga17合金定向凝固试样的择优取向受到阻碍。采用晶体生长速率与固液界面形态关系解释了这一现象。
The preferred orientation of directional solidified sample was interrupted as the growth velocity was 10 μ m / s. The phenomena were explained by the relationship between growth velocity and the solid-liquid interface shape .